The Science Behind Screw Threads: Strength & Grip Explained
Learn how screw threads impact strength and grip. Explore different thread designs, their applications, and how they enhance fastener performance.
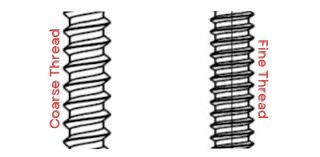
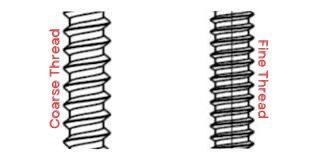
Screw threads are a fundamental aspect of fasteners, playing a crucial role in their performance, strength, and grip. Understanding different thread types and their impact can help engineers, manufacturers, and end-users select the right fasteners for their specific applications.
Types of Screw Threads
Screw threads are primarily classified into two main types: coarse threads and fine threads. Each has distinct characteristics and applications.
1. Coarse Threads (UNC - Unified National Coarse)
Fewer threads per inch (TPI)
Deeper and thicker threads, making them more durable
Better resistance to stripping due to increased thread engagement
Ideal for softer materials such as wood, plastics, and aluminum
Easier to assemble and disassemble, making them suitable for applications requiring frequent adjustments
2. Fine Threads (UNF - Unified National Fine)
More threads per inch (TPI)
Shallower, closely spaced threads, allowing for higher tensile strength
Greater resistance to loosening under vibration due to increased friction
Preferred for precision applications such as aerospace, automotive, and machinery
Stronger in tension, making them suitable for high-stress environments
How Threads Affect Strength and Grip
1. Load Distribution and Tensile Strength
Fine threads distribute load more evenly across a larger number of threads, resulting in higher tensile strength compared to coarse threads. This makes them suitable for applications requiring high clamping force.
2. Shear Strength and Stripping Resistance
Coarse threads have thicker roots and crests, which provide better shear strength and reduce the risk of thread stripping. This makes them ideal for use in materials with lower strength.
3. Grip and Holding Power
Coarse threads have deeper threads that penetrate materials more effectively, offering better holding power in soft materials.
Fine threads create a tighter grip in harder materials and resist loosening due to vibration, which is crucial in precision engineering.
4. Assembly and Maintenance Considerations
Coarse threads are easier to start and assemble, making them more user-friendly in general applications.
Fine threads require more precise alignment and are harder to thread but provide better adjustability and fine-tuning in critical applications.
Choosing the Right Thread for Your Application
For different applications, consider the following recommendations:
Woodworking and soft materials: Coarse Threads (UNC) are the best choice due to their deep penetration and better grip.
Automotive and aerospace: Fine Threads (UNF) offer enhanced tensile strength and resistance to vibration.
Machinery and structural applications: Fine Threads (UNF) are preferred for their higher precision and strength.
General construction: Coarse Threads (UNC) provide ease of use and durability.
High-vibration environments: Fine Threads (UNF) resist loosening, ensuring long-term reliability.
Conclusion
The choice between coarse and fine threads depends on the material, load requirement, and environmental conditions. While coarse threads provide durability and ease of use, fine threads offer better tensile strength and resistance to vibration. By understanding these differences, engineers and manufacturers can optimize performance and reliability in their designs.
At Bait Alnuhas, we provide a wide range of high-quality fasteners designed for various industries. Contact us today for expert advice on selecting the right fasteners for your projects!