Stainless Steel vs. Brass Fasteners: What’s Best for Saltwater Boats?
Choosing between stainless steel and brass fasteners for your saltwater boat? This expert guide compares corrosion resistance, durability, and application tips to help you choose the right option for marine environments.
INDUSTRY-SPECIFIC SOLUTIONS
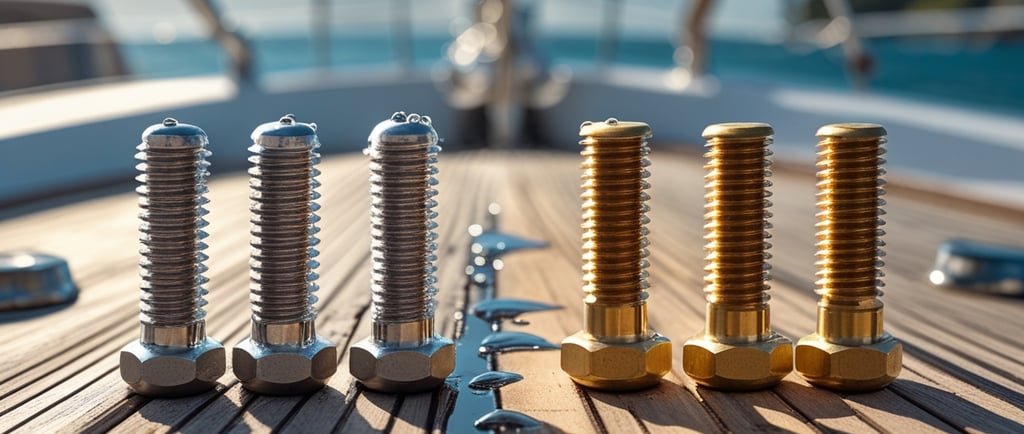
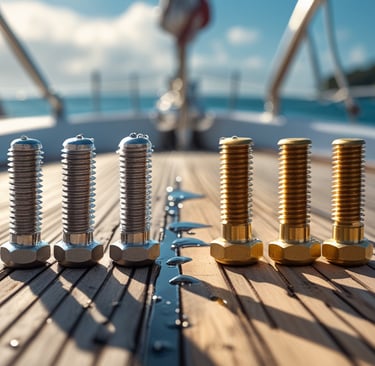
Introduction
Saltwater environments are among the harshest for any material—especially fasteners. Constant exposure to moisture, salt spray, and fluctuating temperatures can cause corrosion, weakening, or even failure. For boat owners and marine professionals, selecting the right fasteners is critical to ensuring safety, longevity, and performance.
Two popular fastener materials—stainless steel and brass—are frequently used in marine settings, but they serve different purposes. This blog compares the two, so you can make an informed decision for your saltwater vessel.
Why Fastener Material Matters in Saltwater
When it comes to fasteners used in or around saltwater, corrosion resistance is everything. Saltwater speeds up oxidation and corrosion processes, especially when fasteners are exposed to air and moisture cycles. A compromised fastener can loosen or break, leading to potential water leaks, structural damage, or mechanical failure.
In marine settings, your fasteners need to:
Withstand corrosion for years
Resist vibration and mechanical stress
Work with a variety of metals and materials
Maintain integrity with minimal maintenance
Let’s explore how stainless steel and brass hold up in these conditions.
Understanding Stainless Steel for Marine Use
Stainless steel is an alloy made primarily of iron and chromium, with some grades also including molybdenum and nickel. The two most common types used in marine applications are 304 and 316 stainless steel.
While 304 stainless steel is widely used for general corrosion resistance, it’s 316 stainless steel that truly shines in saltwater environments. This grade contains molybdenum, which enhances its ability to resist rust and corrosion from chloride exposure, making it ideal for marine use.
Stainless steel fasteners are known for their strength, high resistance to rust, and clean finish. They’re suitable for high-stress components and structural connections. They’re also excellent for deck hardware, hinges, brackets, engine compartments, and any other visible or load-bearing applications on a boat.
Polished stainless steel not only performs well but also looks great, which adds to its appeal for use on visible areas of a boat.
Understanding Brass for Marine Use
Brass is an alloy of copper and zinc, and sometimes includes small amounts of other elements like lead or tin to improve machinability and corrosion resistance. It’s a softer material than stainless steel, but it brings its own strengths—especially for specific tasks.
Brass resists corrosion reasonably well, particularly in less aggressive environments or protected interior areas. Its real strength lies in electrical conductivity and non-sparking properties, making it suitable for marine electrical systems and fuel fittings.
In marine settings, brass is often used in plumbing fixtures, hose fittings, and electrical connectors. However, it’s not recommended for submerged applications or areas directly exposed to saltwater. Over time, brass can undergo a process called dezincification, where zinc leaches out of the alloy, weakening the structure and leading to failure.
Because of this, brass should be reserved for applications where it remains dry or only encounters mild moisture—never for underwater use.
Which One Is Stronger and More Durable?
Stainless steel fasteners are significantly stronger than brass ones. They provide higher tensile and shear strength, making them suitable for structural and high-load applications. If your fastener needs to bear a lot of stress—like supporting deck fittings or securing hull components—stainless steel is the right choice.
Brass, on the other hand, is softer and more prone to deformation under pressure. While it’s easier to cut, drill, and shape, it’s not designed for heavy loads or constant mechanical vibration.
What About Corrosion Resistance?
For saltwater boats, corrosion is the primary enemy. Stainless steel—especially 316 grade—offers superior resistance to salt and moisture. It can handle years of exposure without rusting or pitting, especially if cleaned periodically.
Brass has moderate corrosion resistance and is best used in indoor or protected spaces. In salt-heavy environments, especially below the waterline, it simply won’t last as long. You may see tarnishing, surface corrosion, or even structural breakdown over time if used in the wrong place.
Risks of Galvanic Corrosion
A common problem in marine fastener installation is galvanic corrosion, which happens when dissimilar metals are in contact in a wet or conductive environment. For example, stainless steel can cause accelerated corrosion of softer metals like aluminum or brass if not properly isolated.
To avoid this:
Don’t mix brass and stainless fasteners in the same area.
Use isolation washers, nylon spacers, or marine-grade sealants when mixing metals.
Match your fasteners with compatible base materials whenever possible.
Where Each Material Excels
Use stainless steel fasteners when:
The area is exposed to saltwater or weather
Strength and load-bearing are important
A polished, rust-free appearance is preferred
Components are above or below the waterline
Use brass fasteners when:
You need corrosion resistance in low-moisture environments
Electrical conductivity is required
Components are inside the boat (like plumbing or wiring)
You want a non-sparking solution for fuel systems
Expert Tips for Longer Fastener Life
Choose 316 stainless steel for the best marine protection.
Avoid using plain brass in any submerged or salt-exposed area.
Inspect fasteners regularly, especially in high-stress or waterline zones.
Use anti-seize lubricants when installing stainless steel fasteners to prevent galling.
Don’t mix metals without using isolation techniques.
Rinse down hardware with fresh water after heavy saltwater exposure.
Use fasteners rated as “marine-grade” to ensure durability and compliance.
Conclusion: The Right Fastener for the Job
When it comes to saltwater boats, your choice of fastener material isn’t just about cost—it’s about safety, reliability, and long-term maintenance. Stainless steel, especially 316 grade, is the top choice for nearly all structural, submerged, and exterior uses. It resists corrosion, handles load stress, and maintains its appearance for years.
Brass, while useful in specific cases like electrical fittings and interior applications, should be used with care and only in environments where it won’t be exposed to saltwater or moisture long-term.
When in doubt, stainless steel is your best bet for marine durability. It may cost a bit more upfront, but it pays off with longer life and fewer headaches down the line.
Looking for marine-grade fasteners?
At Bait Alnuhas, we supply high-quality 316 stainless steel fasteners perfect for boatbuilders, repair specialists, and DIY marine enthusiasts. Contact us for expert recommendations or bulk orders customized for your needs.