Heavy-Duty Bolts and Nuts for Structural Applications: How Screw Head Types Impact Performance and Assembly
Explore how different screw head types like hex, square, and socket impact strength, torque, and assembly in structural construction and steel applications.
PRODUCT-SPECIFIC
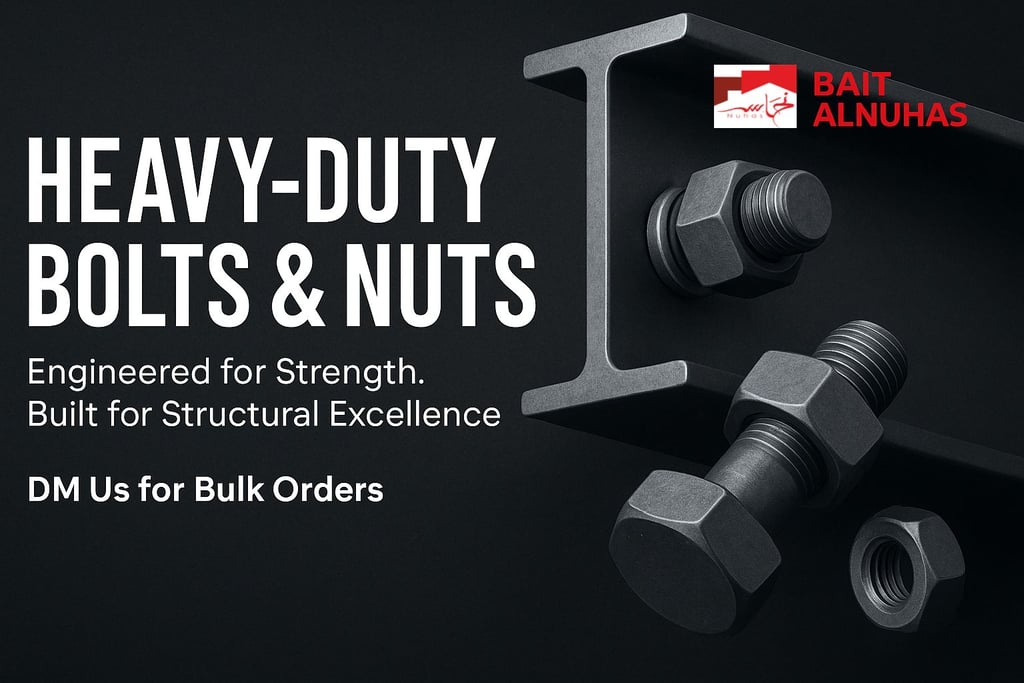
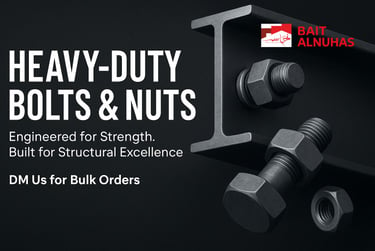
Introduction
In structural engineering and high-load construction environments, the smallest components often carry the greatest responsibility. Heavy-duty bolts and nuts serve as the backbone of stability in steel frameworks, bridges, towers, and industrial plants. Their performance can directly influence the safety, durability, and compliance of an entire structure.
But while much attention is given to the bolt’s strength or material grade, one often-overlooked element plays a crucial role in both installation efficiency and structural integrity: the screw head type.
From torque distribution to surface flushness and tool compatibility, the design of a fastener's head can dramatically impact long-term performance. In this post, Bait Alnuhas, a trusted industrial fasteners supplier in the MENA construction fasteners market, offers expert insight into selecting the optimal screw head type for structural bolts and nuts.
Understanding Heavy-Duty Bolts and Nuts
Key Materials for Structural Fasteners
Heavy-duty bolts and nuts used in construction must endure extreme loads, vibrations, and environmental conditions. That’s why choosing the right material is foundational:
Carbon Steel
Common in construction bolts due to its strength and affordability. Often coated (e.g., galvanized) to improve corrosion resistance.Stainless Steel
Offers superior corrosion resistance, ideal for marine, infrastructure, and oil & gas projects, especially in coastal or chemically aggressive environments.Alloy Steel
High-performance material for demanding structural applications, providing enhanced strength, fatigue resistance, and reliability under dynamic loading.
Applications Across Industries
Construction – Steel-to-steel connections, beam joints, and base plates in high-rise buildings and industrial warehouses.
Infrastructure – Bridges, tunnels, railway systems, and highway structures requiring long-term resilience.
Marine & Offshore – Fasteners exposed to saltwater, where corrosion resistance and strength are non-negotiable.
Oil & Gas – Heavy flange connections, pipeline supports, and equipment mounts subject to intense vibration and pressure cycles.
Screw Head Types: Performance & Assembly Considerations
The design of the screw or bolt head influences how the load is distributed, how easily the fastener can be installed, and how well it integrates into the structure.
1. Hex Head
Description: A six-sided head designed for wrenches or sockets.
Common Use: Structural steel frameworks, machinery bases.
Torque Distribution: Excellent torque handling.
Ease of Installation: High; compatible with power tools and manual wrenches.
Tool Compatibility: Universal.
Surface Flushness: Not flush—head protrudes.
Structural Load Impact: Highly reliable under tensile and shear loads.
Pros:
Easy to grip and tighten.
Widely accepted in standards (e.g., ASTM A325, ISO 4014).
Cons:Not suitable for flush surfaces or concealed joints.
2. Socket Head (Allen)
Description: Cylindrical head with internal hex drive.
Common Use: Machinery, enclosed or space-restricted areas.
Torque Distribution: Good but requires precision tightening.
Ease of Installation: Moderate—requires Allen keys or hex drivers.
Tool Compatibility: Limited to hex key sizes.
Surface Flushness: Head may protrude, but variants exist for countersinking.
Structural Load Impact: Suitable for medium-load assemblies.
Pros:
Clean appearance, compact.
Ideal where lateral space is restricted.
Cons:Lower torque limits than external hex heads.
3. Flat Head
Description: Conical head designed to sit flush within the surface.
Common Use: Countersunk joints, flooring brackets, architectural finishes.
Torque Distribution: Moderate; stress concentrated around head taper.
Ease of Installation: Requires countersinking.
Tool Compatibility: Typically Phillips or slotted.
Surface Flushness: Perfectly flush.
Structural Load Impact: Best for light to moderate axial loads.
Pros:
Aesthetically pleasing.
Prevents snagging or tripping hazards.
Cons:Lower load-bearing than hex or flange heads.
4. Pan Head
Description: Low-profile, rounded head with a wide bearing surface.
Common Use: Electrical, light-duty framing.
Torque Distribution: Even but limited torque tolerance.
Ease of Installation: Easy with standard screwdrivers.
Tool Compatibility: Phillips, slotted.
Surface Flushness: Slight protrusion.
Structural Load Impact: Light-duty only.
Pros:
Spreads load over a broader surface.
Cost-effective.
Cons:Not designed for high structural loads.
5. Button Head
Description: Rounded head with internal hex drive; stylish, low-profile.
Common Use: Safety guards, panels.
Torque Distribution: Lower than socket heads.
Ease of Installation: Requires Allen tools.
Tool Compatibility: Internal hex only.
Surface Flushness: Slightly protruding.
Structural Load Impact: Limited.
Pros:
Smooth appearance.
Reduces risk of catching on equipment or clothing.
Cons:Not load-rated for critical structural connections.
6. Round Head
Description: Traditional dome-shaped head, often slotted.
Common Use: Decorative, light mechanical joints.
Torque Distribution: Low.
Ease of Installation: Easy with manual tools.
Tool Compatibility: Slotted or Phillips.
Surface Flushness: Protrudes.
Structural Load Impact: Minimal.
Pros:
Simple and cost-effective.
Cons:Not suitable for high-stress environments.
7. Flange Head
Description: Hex or round head with an integrated flange acting like a washer.
Common Use: Automotive, steel structures, equipment mounting.
Torque Distribution: Excellent—flange spreads the load.
Ease of Installation: High; prevents loosening.
Tool Compatibility: Standard hex/socket tools.
Surface Flushness: Slightly raised.
Structural Load Impact: High—reduces bolt pull-through.
Pros:
Enhances clamping force.
Reduces need for additional washers.
Cons:Slightly higher cost.
8. Truss Head
Description: Extra-wide, low-profile head offering broad surface coverage.
Common Use: Sheet metal, insulation panels.
Torque Distribution: Low to moderate.
Ease of Installation: Easy with screwdrivers.
Tool Compatibility: Phillips or slotted.
Surface Flushness: Wide but shallow protrusion.
Structural Load Impact: Limited to light-duty.
Pros:
Prevents material damage on thin substrates.
Cons:Not designed for high-load environments.
Choosing the Right Head Type for Structural Applications
When selecting the best screw or bolt head for a structural application, professionals should evaluate the following:
1. Structural Load Demand
Use hex head, flange head, or socket head for high-load and shear-resistance applications.
Avoid flat, button, or pan heads for critical joints.
2. Accessibility Constraints
Socket head and button head are ideal where lateral tool access is limited.
Use flat head when fasteners must sit flush for movement clearance or design needs.
3. Compliance with Safety Standards
Ensure selected bolts comply with international standards:
ASTM A325, ASTM A490 (structural bolts)
ISO 898-1 (mechanical properties)
DIN 931/933 (metric fasteners)
4. Environmental Exposure
In marine, offshore, or chemical environments:
Choose stainless steel or coated carbon steel.
Avoid head types prone to corrosion traps (e.g., deep socket heads without sealing).
Why It Matters: Real-World Case Studies
Case Study 1: Steel Bridge Construction in Coastal UAE
A contractor selected hex flange bolts for beam-to-column joints on a pedestrian bridge exposed to sea air. The built-in flange eliminated washer use, reducing installation time by 18% and ensuring uniform load distribution. After 5 years, inspections showed zero loosening or corrosion, confirming performance in marine environments.
Case Study 2: High-Rise HVAC Support Brackets
A structural engineer initially specified pan head screws for HVAC duct supports. Post-installation, excessive vibration caused loosening and failure. Upon switching to socket head cap screws with lock washers, stability improved, and no incidents were reported in subsequent quarterly checks.
Conclusion & Call to Action
Heavy-duty bolts and nuts are not just hardware—they are the unseen pillars that uphold the safety and longevity of your structure. Understanding the differences between types of screw heads can drastically improve bolt assembly performance, reduce installation errors, and enhance structural reliability.
For construction professionals in the GCC and MENA region, the right fastener starts with a trusted supplier. Bait Alnuhas is your go-to expert for MENA construction fasteners, offering a wide range of structural bolts and nuts, including hex, flange, and socket head designs that meet or exceed international standards.